What are non-destructive tests?
Inspection techniques are used for the detection and evaluation of possible discontinuities that may exist both on the surface and inside the metallic materials (rolled plate, forged material, castings, welding, etc.) that are used For the manufacture of pressure vessels, atmospheric tanks, valves, shafts, heads, pipes, etc.
These techniques are called Non Destructive Tests because when applied, the materials are not destroyed or their physical, chemical, mechanical and / or dimensional properties are affected.
The stages or situations in which Non-Destructive Testing are applicable are described below.
- Raw Material Receipt
- Manufacturing processes
- Machining or Final Assembly
- Welding processes
- Weld repair processes
- Preventive maintenance
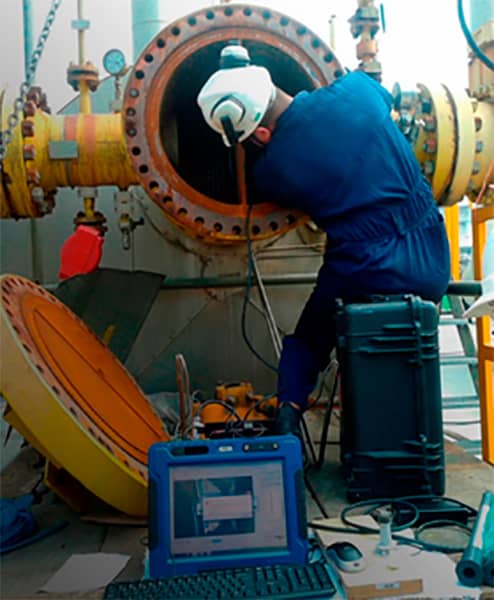
Importance of visual inspection
It can be said that the visual inspection is an instinct that owns the human being; In man most of the information he receives from the outside world, he does so through the «visual» channel. The large number of experiments that are performed or practiced are usually ultimately visible or optical.
Such information is often indirect: since the sense of sight works or provides moving sensations of the clock hands from which a physical reality occurs. The view however can provide more information that can not be achieved by other means. In addition visual inspection is the NON-DESTRUCTIVE TEST par excellence; The light being its physical agent does not produce any damage in the majority of the materials. Only a small fraction of the light that can be transmitted by the object is sufficient for the purpose of obtaining the information necessary to transmit it directly to the brain, the subject of the visual inspection is important in itself, although being so Recognizes as such, however it is important to limit its scope if one wishes to go to distant places. Technically leaving the visual inspection in the examination with the naked eye is not enough, on the contrary it leads to the correct diagnosis, which undoubtedly tends to be somewhat exaggerated; This technique is a stage of NDT, which is accompanied by other practices, but it is very important to take into account that the staff that does not have a defective vision.
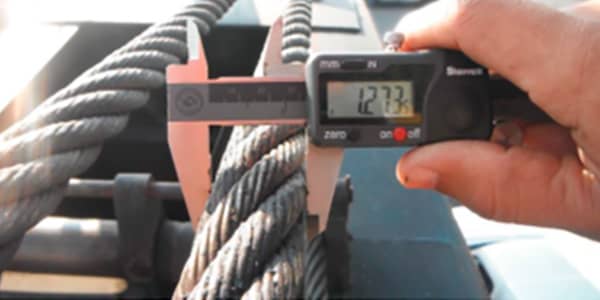
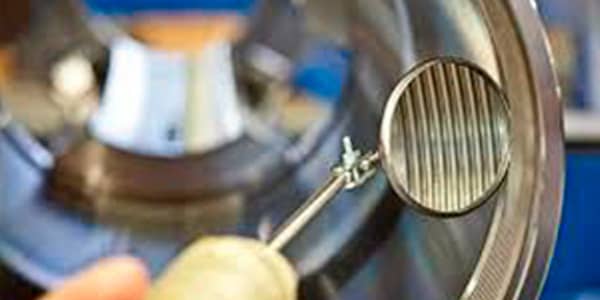
Importance of direct visual
It is done at a short distance from the object, taking full advantage of the inspector’s natural visual ability.
Magnifying lenses, microscopes, lamps, or flashlights are used, and measuring instruments such as calipers, micrometers, and gauges are often used to measure and classify the conditions encountered.
Importance of remote visual inspection
It is used in those cases where there is no direct access to the components to be inspected.
It is widely used in the industry to verify the internal state of engines, turbines, compressors, boiler pipes, heat exchangers, tanks and valves, among others.
Rigid or flexible, videoscopic and fiberscopic (optic fiber) borescopes are used, with which it is possible to reach most of the internal cavities and places inaccessible to the inspector.
Magnetic particle test
This Non-Destructive Testing method is based on the physical principle known as magnetism, which is mainly exhibited by ferrous materials such as steel and consists of the capacity or power of attraction between metals. That is, when a metal is magnetic, it attracts other metals that are equally magnetic or with the capacity to become magnetized at its ends or poles.
Testing with penetrating liquids
The penetrant liquid inspection method is a non-destructive test which is intended to locate defects on the surface or inside of a material without deteriorating it. This is a practice that is used for its ease and speed with commercial sprays that are applied on parts that are not subject to an excessive degree of exigencies.